Gillette Razor Blades in the Adjustable Era
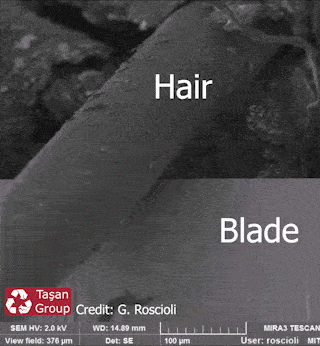
UPDATE Research on why razor blades dull from Massachusetts Institute of Technology Aug 6, 2020. Patents have been applied for which will allow for the manufacture of blades which provide more homogeneity by compressing the steel at the blade edge instead of heating it causing less chipping and micro-fractures that lead to edge loss. However, heating is essential to PTFE application which Gillette found to be a more important factor in blade durability or shave comfort.
Science Magazine Academic Paper - How Hair Deforms Steel
So, I have been getting more interested in the innovations in razor blade manufacturing technology and why and how those innovations were implemented. I came across news articles when researching Meyer Shnitzler (1912 - 2007), the VP of R&D at Gillette from 1933 till 1967. He, among other things, invented the DE razor blade dispenser with used blade slot, the plastic razor case, the Toggle and Bottom Dial Adjustable razors and he also invented the Silicon coating on Blue Blades which caused them to be renamed Super Blue Blades.
Apparently, on reading the patent application (US2937976) for the silicon coating and news interviews of Mr Shnitzler, men were not adequately prepping their faces prior to shaving and this was causing pain and irritation while using Gillette's product. Mr Shnitzler, in his research lab, started experimenting with various steel blade configurations that would allow for sharper blades to be produced. But guess what? He determined blade sharpness could not readily be detected by the shaver and sharper blades did not alleviate the pain and irritation from poor prep. It turns out that, according to Mr. Shnitzler, the improperly moistened whisker is harder to cut and the hair itself will adhere to the steel, as it is being cut, causing the hair follicle to be pulled with the consequent pain/tugging feeling. A chemical engineer by training at MIT prior to coming to Gillette, Mr Shnitzler's solution to the problem was an organic silicon coating to the steel so that the protein in the hair would not adhere to the steel; yielding a better cutting action with less pulling at the follicle. The Super Blue was born (1959).
Later, Gillette patented a process for manufacturing stainless steel blades but sat on the development. Wilkinson beat Gillette to the market with the first stainless steel blade, which had the benefit that it could last longer without corroding. However, Gillette was not in a rush to bring stainless steel blades to market in that there was no improvement to the shave inherent in a less corrodable base metal. Also, Wilkinson had to pay royalties (after a law suit) to Gillette to use their patented technology to manufacture the stainless steel blades. Within a couple of years the competitor's stainless steel blades were substantially cutting into Gillette's dominant market position and their market share went from 70+% to 60+%. Gillette then introduced their stainless blades (1962). Gillette's next innovation was the Super Stainless Blade (1965). This blade dubbed "The Spoiler" had a "miracle plastic coating baked onto the edge" - this was a PTFE coating with similar properties as the silicon coated Super Blue blades from 1959. However, the heat necessary to apply the PTFE coating, necessary for better cutting action, caused the underlying metal to weaken and lose its anti-corrosive properties. It was discovered that adding a corrosive resistant noble metal such as platinum, gold or rhodium solved this problem. However, these metals are soft and needed to be alloyed with chromium, titanium or tungsten. Next came platinum-chromium alloys and PTFE coating for stainless steel (US3682795) from Gillette as the Platinum Plus (1969). Well, long story short, Gillette abandoned the Double Edge razor blade market selling off their manufacturing equipment to whoever would buy it (read India, Russia, etc) in pursuit of proprietary (read expensive/profitable) multi-blade cartridges.
It is my belief that by 1969 Gillette had mastered razor blade technology, the technology was readily available to competitors and profits would soon go away to lower cost competitors. But, as far as the technology goes, today there is nothing new or better in what gets delivered to the double edge blade customer.
If you believe the words of Mr. Shnitzler and the truth of the patent applications, we have the following takeaways:
1) Carbon steel Blue Blades are definitely worse shaving than carbon steel Super Blue blades.
2) Un-PTFE coated stainless steel blades are definitely worse shaving than carbon steel Super Blue blades.
3) PTFE coated stainless steel blades without a hardening alloy have no longevity benefit over carbon steel blades.
4) The absolute best blade for shaving performance and longevity is made with a stainless steel blank with noble metal/denser metal alloy edge that is then coated with PTFE.
5) All the talk about needing super sharp blades is fiction (a PTFE coating is superior to extra sharpness and sharp pointy edges wear down quicker.)
6) Prep and moisturize your darn face properly!!!!!
7) Yes, Tungsten is great to alloy with and is a great dense metal (70% denser than lead), but really, why pay so much for the Personna 74 Tungsten Plus? It is not worth $6 per blade for some extra longevity with no better shaving performance than the cheaper chromium. And, if the Personna 74 Tungsten (no Plus) has no PTFE coating, it is no good! Certainly don't pay so much for the non-plus version!
As far as the best blade to get from above (#4) look for stainless steel that has platinum, osmium, iridium, palladium, rhodium, ruthenium or gold that has been alloyed with chromium, titanium, manganese, niobium, molybdenum, tantalum or tungsten on their cutting edge that has a PTFE coating.
So, I built a chart based on the technological innovations made by Gillette. The highest blades on the chart are the best. The lowest are the worst. Grading scale was arbitrary but accurate relative to the other blade products on the chart. Interesting that the Gillette Stainless blade was a real clunker! Not even as good as the Super Blue which preceded it, but it was replaced by the Super Stainless blade. The pan-ultimate blade was the Platinum-Plus.
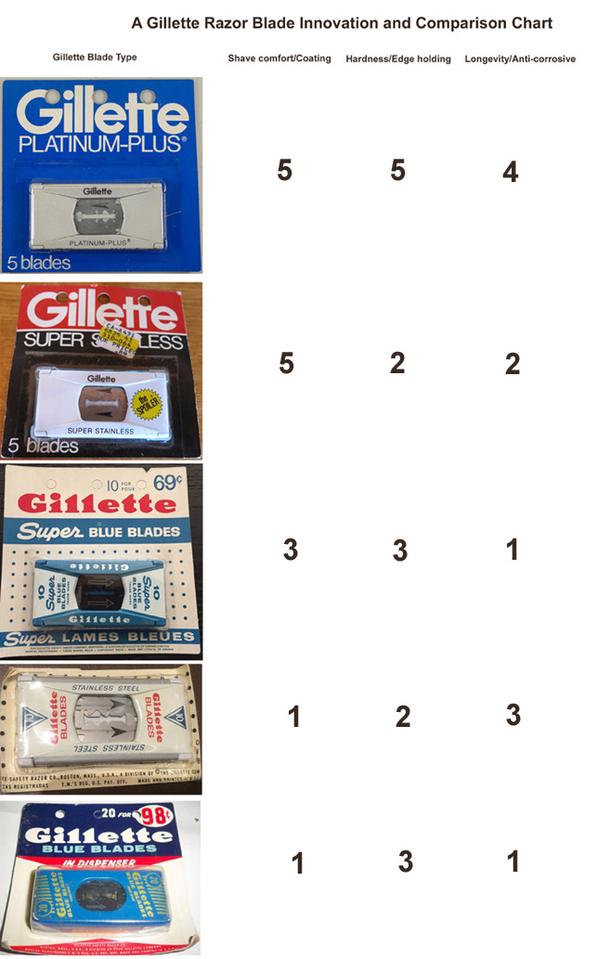
From the perspective of historical innovation at Gillette, the whole idea of sharpness versus smoothness was discarded by Mr Shnitzler. I think on my reading of his work, he felt that there was an acceptable range of honing a blade that would balance cutting performance and edge durability, but that these characteristics were not detectable, for the most part, by his research subjects in his lab. Other factors, such as face preparation and blade coatings had much more visible or detectable consequences on shaving closeness and comfort. Mr Shnitzler came up with his "Drag Theory" based on his research and developed the "Organ Osiloxane Gel Coated Razor Blade" rather than tinkering around with blade sharpness when he found that that did not work. Common sense will imply a sharper blade is better if you have a coarse beard and duller is better when you have sensitive skin, but this is not what he found to be the case when looking for ways to manufacture a blade that would provide the greatest customer satisfaction and therefore market share and resultant profits for his company. As far as his take on carbon steel (CS) versus stainless steel (SS), he did not believe SS had an advantage over CS as far as sharpness (CS from my reading is better), the advantage of SS is corrosion resistance. And, SS may even be worse than CS when it comes to "drag" or adhesion to the whisker hair which causes pulling and discomfort. Gillette's research on blade coatings to improve shave comfort (especially needed for SS blades), I believe lead them to adoption of a more superior coating than silicon which was PTFE or variant thereof. Fluorocarbon coating yielded a "remarkable increase in shaving effectiveness... and decreased pull." But, again, the heat necessary for application of PTFE ruins the SS metal softening it. Hence the need for LESS sharpness to strengthen the edge and the application of a noble metal to improve corrosion resistance. The noble metals however flake off carrying away the PTFE coating and therefore need to be alloyed with denser metals. The winner, as far as Gillette was concerned when all factors were considered was Platinum-chromium alloys applied to stainless steel - not Iridium, Tungsten or Titanium which can be or was seen marketed by other companies - and not carbon steel either.
Final point, Gillette was well aware that different customers may have needed different products. This resulted in the development of the Adjustable Razor - pinnacle of their thoughts on the variable needs of the shaving consumer population. However, once they developed the Platinum-Plus stainless steel blade they ran with it and it exclusively for years and years. If they truly believed YMMV, why the heck didn't they offer 5 or 6 or 9 different types of double edge razor blades all at the same time. This would have greatly improved customer satisfaction if it was needed. But no, they did not go this route at all. So, what does this say about the reality of all the different razor blades being offered today. Is it really YMMV or is it all really poor prep techniques? That is, do we really need more than just one blade type?
What does cooking have to do with shaving? A lot!
So, I have been doing some research into coatings on razor blades and why they are there. Gillette discovered in 1958 (US2937976) that a Silicon Coating on the Blue Blade (Super Blue) yielded a "remarkable reduction in pull." However, they specifically said they did not understand why? They also patented (US3071856) in 1959 the Flurocarbon (PTFE) coating. Again, even with their understanding of the Silicon coating, the PTFE coating yielded yet again a "remarkable increase in shaving effectiveness." However, no explanation as to why!?
After, doing some research, I believe that there is a special "stickiness" that occurs between a whisker hair as it is being cut and the uncoated steel. The Keratin protein in the hair and the steel adhere to each other and this is experienced as a pulling at the follicle and discomfort etc. This adhesion occurs at the atomic level (or molecular level) and no amount of blade polishing will reduce the friction.
To understand this adhesion, I stumbled upon why metal pans are coated with PTFE. My research led me to cooking science. Apparently proteins are highly adhesive to fry pans. Who knew eggs stick - ha ha?! Even highly polished uncoated stainless steel ones stick. The solution to eliminate the "stickiness" is to put a barrier between the metal and the protein. So, if you want to understand why a modern PTFE coated razor blade is better than one of the old crappy Gillette Blue Blades, look to the pans man, look to the pans.
From Wikipedia - Surface chemistry of cooking: "When meat cooks the proteins on the surface of the meat denature because of the heat. This means that many of the secondary bonds that give the proteins their shape are broken. The protein molecules want to reform those interactions to return to their most thermodynamically stable state. Two opportune locations for the surface proteins to bind are the oil and the surface of the pan. Meat sticking to the bottom of the pan is caused by the interactions between proteins on the surface of the meat binding with the molecules on the surface of the pan. Since the proteins and the surface of the pan, all have a significant polarity, the force of their interactions can be high."
So, my reading of this is that heat does have something to do with it. It denatures the protein causing it to want to bind to the surface of the pan to become thermodynamically stable. All this begs the question - does the cutting of hair break the secondary bonds that give the proteins their shape, thereby ALSO causing an adhesion effect (ie causing the hair to stick to the surface of the blade)?
From Quora - What happens when you cut through matter? "Essentially, a knife is a tool for concentrating force into a very small area, creating a massive amount of pressure on a single line. Every molecular bond has a limit to how much stress it can take. If the force you apply is concentrated on few enough bonds that it exceeds their strength, then those bonds break. Most of the things that you'd cut with a knife are held together by covelant bonds, which connect long chains of organic molecules. When those bonds break, you have unstable molecules hanging off the end, which are very reactive. They will tend to very quickly react with whatever is at hand, including each other. The dangling ends very quickly resolve themselves, so if you remove the knife and put the pieces back together, they have no driving force to rejoin. Chemically, you've forced a single mass to convert into two separate masses."
So, my reading of this is the cut ends ARE VERY REACTIVE and as such will want to bind to the molecules on the surface of the blade - thereby causing the pulling or tugging at the follicle.
So why doesn't the sheared hair stick to a PTFE coated blade?
From Explain That Stuff - Nonstick Pans "PTFE is chemistry's equivalent of an introvert. It likes its own company, but it doesn't like other molecules all that much. Put a load of PTFE molecules together and they clump and stick together like spaghetti. In physics terms, we say there are strong cohesive forces between them. When you see a drop of rain sticking to a pane of glass, hanging in mid-air like a climber on a cliff, what you're seeing is cohesive forces in action. There are strong forces of attraction inside the water tugging its molecules inwards into the shape of a drop. But you're also seeing another kind of force too. There are adhesive forces holding the water molecules to the molecules in the glass. These are called van der Waals forces (pronounced: 'van dur varls') forces, named for the Dutch physicist Johannes Diderik van der Waals (1837–1923) who discovered them (and earned himself a Nobel Prize in the process). On the microscopic scale, van der Waals forces are what cause friction. Imagine a legion of invisibly tiny fingers helping the water molecules cling to the glass. That's what van der Waals forces are like.
In PTFE, the cohesive forces are strong, but there are virtually no adhesive, van der Waals forces between the PTFE polymer molecules and anything that comes into contact with them. Try putting a single drop of water on a nonstick pan. Now turn the pan vertically so the drop has to cling like a climber on a cliff. How long does it stay there? No time at all: it cannot stick to the surface because the weight of the water is many times greater than the frictional, van der Waals forces—so the drop screeches immediately to the bottom of the pan. And notice that it doesn't smear like a raindrop falling down glass. The frictional forces are so low that it stays as a drop as it falls. It's still a drop when it gets to the bottom."
QED
There you have it. The reason why a coated razor blade is more comfortable to shave with than an uncoated razor blade is the PTFE has virtually no adhesive forces between it and the ruptured hair protein bonds that are desperately trying to cling to something. In an uncoated blade that something is the blade and such adhesion causes the hair to be pulled at the follicle causing pain and discomfort.